Cobot Inspection Cells: A Paradigm Shift in Automated Quality Control for Manufacturers
- sethwithers9
- Jun 17, 2024
- 2 min read
Modern manufacturing necessitates rigorous quality control processes to ensure consistent product integrity. Traditional inspection methods, often reliant on human oversight, are susceptible to fatigue-induced errors and inconsistencies. Collaborative robot (cobot) inspection cells present a compelling solution, offering a paradigm shift in automated quality control.
Advantages of Cobot Inspection Cells
Enhanced Measurement Precision and Repeatability: Cobots surpass human capabilities in performing inspections with exceptional precision and unwavering repeatability. This eliminates human error and guarantees consistent quality control throughout production runs.
Improved Production Efficiency: The tireless nature of cobots allows for extended periods of operation without fatigue. This frees up human inspectors for more complex tasks, ultimately leading to increased production throughput.
Cost Reduction: Automating inspection tasks minimizes the need for additional human inspectors, resulting in significant labor cost reductions. Additionally, cobots represent a cost-effective alternative to traditional industrial robots.
Enhanced Safety: Collaborative robots are inherently designed for safe human-robot interaction, minimizing the risk of workplace injuries for human personnel.
Adaptability and Reconfigurability: Cobot inspection cells boast remarkable adaptability. They can be readily programmed for diverse inspection tasks and effortlessly redeployed to accommodate dynamic production requirements.
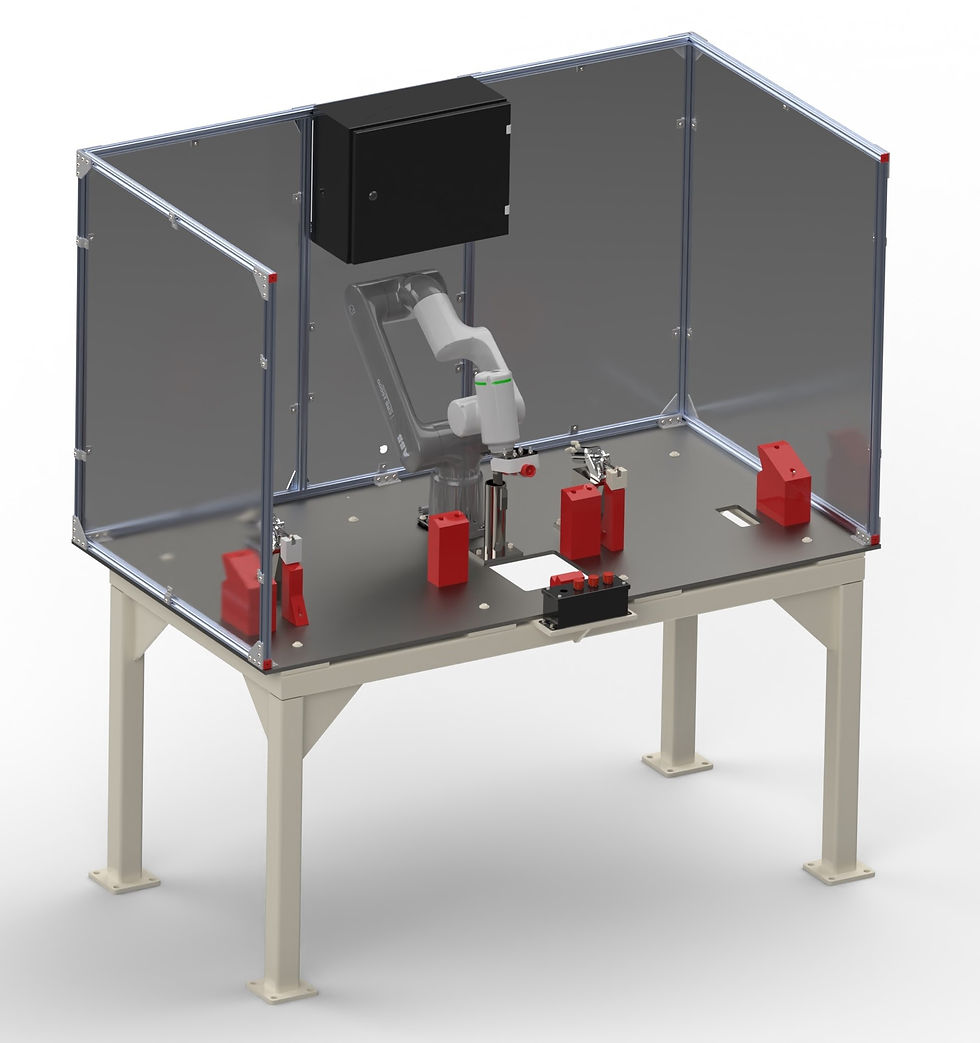
The Importance of Custom Fixturing
To maximize the effectiveness of cobot inspection cells, especially when dealing with parts of varying shapes, sizes, or complexities, custom fixturing plays a crucial role. Custom fixturing refers to the design and fabrication of specialized holding devices that securely position and orient parts within the cobot's workspace.
Precision Part Presentation: Custom fixturing ensures consistent and precise part presentation for the cobot's inspection tools, enabling accurate and repeatable measurements and defect detection.
Improved Cycle Times: Efficient fixturing facilitates faster loading and unloading of parts, optimizing the cobot's cycle time and maximizing inspection throughput.
Enhanced Process Repeatability: By eliminating manual part positioning variations, custom fixturing guarantees consistent inspection processes, leading to reliable quality control data.
Safety and Ergonomics: Well-designed fixtures can safeguard human workers by minimizing the need for manual handling of parts during the inspection process. Additionally, ergonomic fixtures can reduce worker fatigue and strain.

Applications of Cobot Inspection Cells
Visual Inspection: Cobots equipped with vision systems excel at inspecting parts for surface defects, dimensional accuracy, completeness, and proper labeling.
Dimensional Measurement: When equipped with specialized sensors, cobots can precisely measure parts and ensure strict adherence to pre-defined specifications.
Non-Destructive Testing: Cobots can be integrated with technologies like eddy current testing or ultrasonic inspection, enabling the detection of internal material flaws.
Assembly Verification: Cobots can verify the correct and secure assembly of components within a product.
Why KTM Solutions for Your Cobot Inspection Cell Needs?
KTM Solutions has experience designing and implementing cobot inspection cells tailored to your specific manufacturing requirements. Our team of engineers will work closely with you to understand your needs and develop a cost-effective solution that optimizes your quality control processes.
Comments